Our History
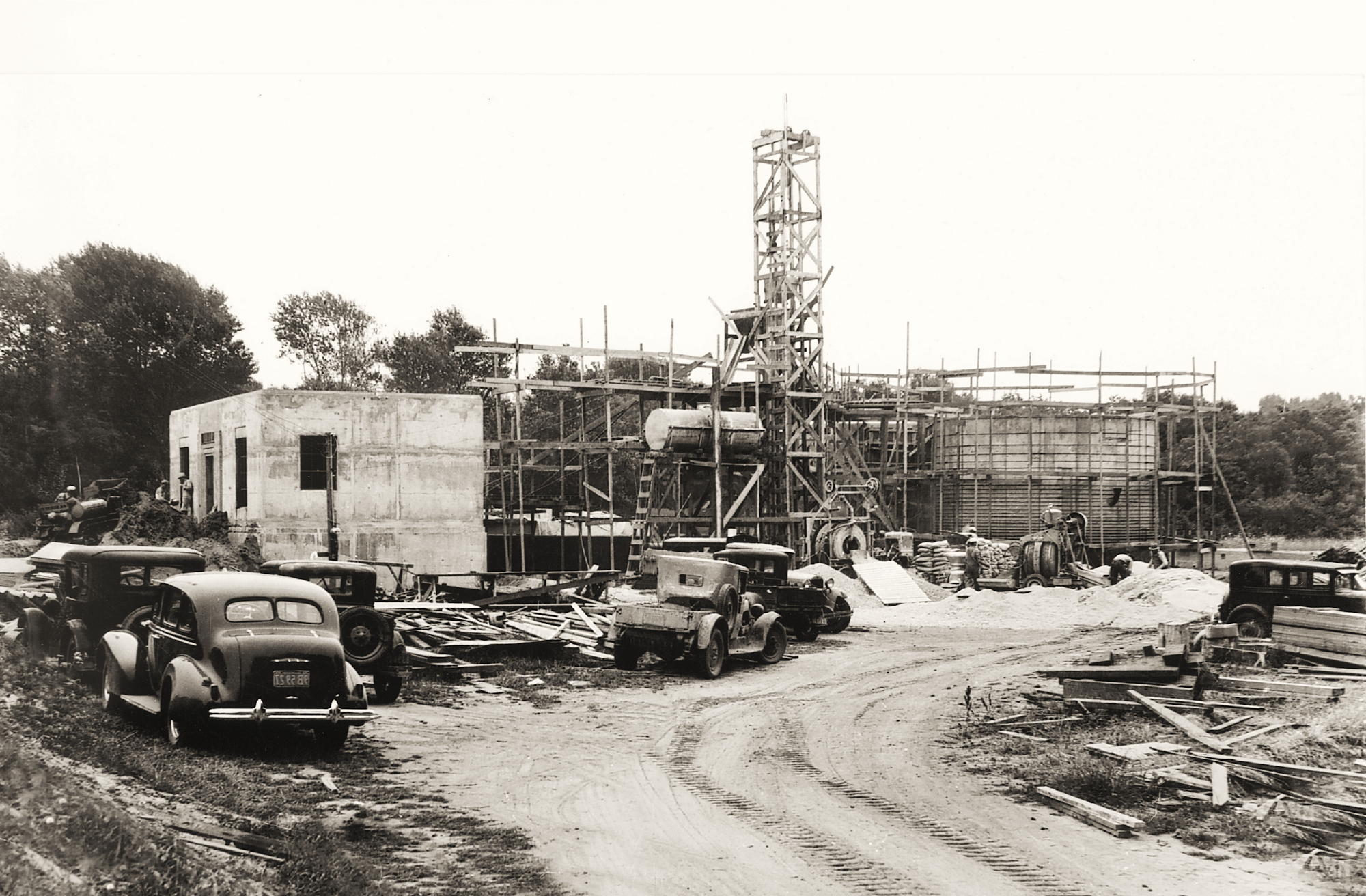
The Carmel Area Wastewater District was formed as the Carmel Sanitary District in 1908. At that time, the District provided septage facilities for the village of Carmel-by-the-Sea.
Over the years the District has grown to where it now provides collection, treatment and disposal of wastewater for 11,000 people within the District and treatment and disposal for an additional 4,500 people in Del Monte Forest.
The District treats wastewater from Carmel and surrounding areas providing advanced treatment to almost drinking water standards. Almost all treated wastewater is sent to Del Monte Forest where it is used to irrigate seven world famous golf courses including Pebble Beach, Poppy Hills and Spanish Bay.
The District serves an area bounded by Carmel Bay to the west, Carmel Highlands on the south and Del Monte Forest on the north. Service extends as far east as Quail Meadows and Del Mesa Carmel.
The District also maintains about eighty-three miles of sewers within the existing service area. The treatment plant is located one-half mile west of Highway One and adjacent to the Carmel River.
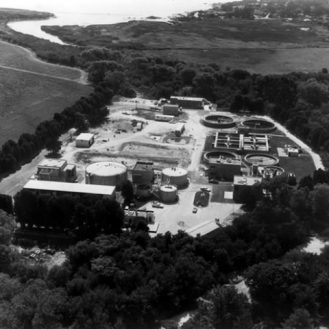
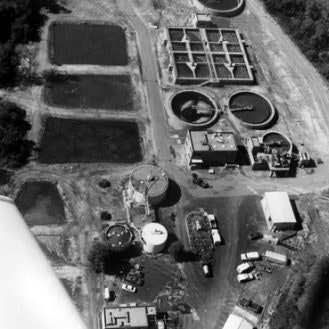
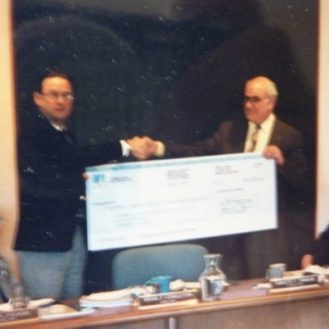
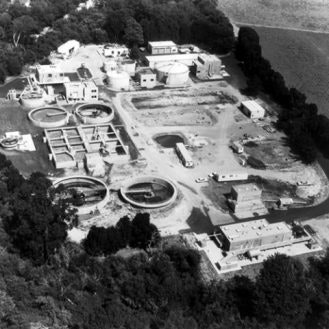
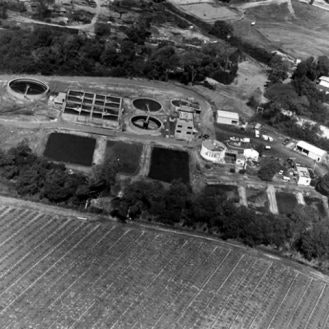
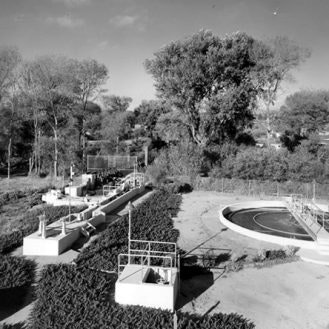
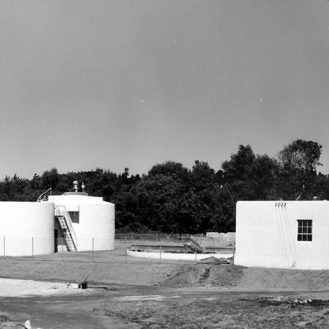
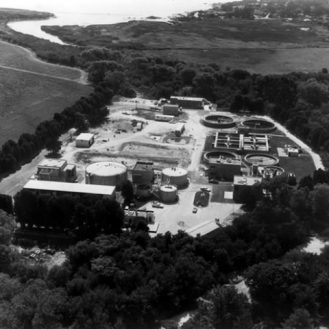
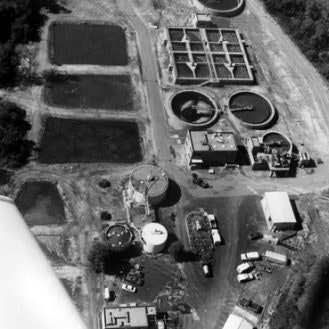
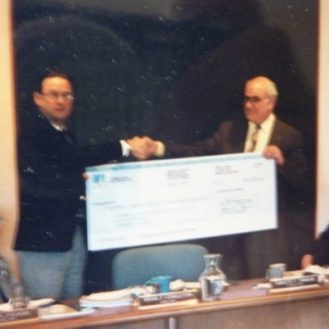
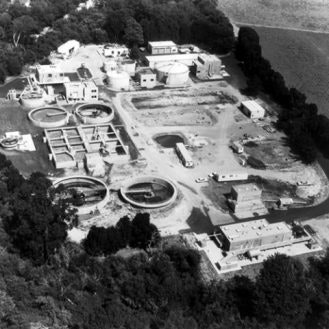
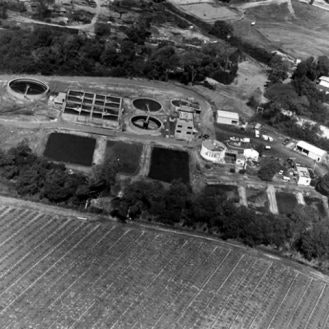
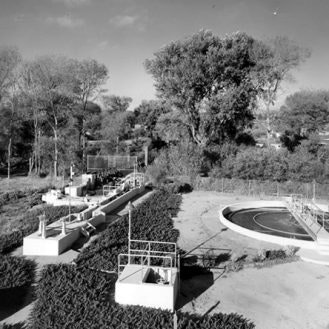
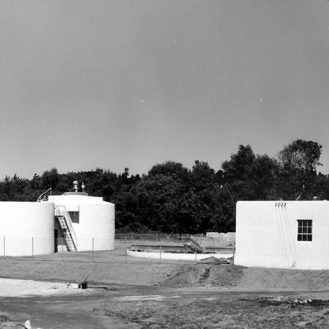