Protecting the Environment and Sustainability Leadership
Turning wastewater into three valuable resources:
Turning Wastewater Into Reclaimed Water
The District is constantly striving to protect the environment by reducing discharges into Carmel Bay and by reducing groundwater pumping from the Carmel Valley aquifer. Prior to building the Reclamation Project in 1995, 100% of the wastewater that entered the plant was only treated to the secondary level, disinfected and then was discharged into Carmel Bay. Since 1995 the wastewater is now treated to the higher tertiary level and is distributed to all seven of the golf courses in the Del Monte Forest (Pebble Beach Golf Links, Spyglass Hill, The Links at Spanish Bay, Peter Hay, Cypress Point, Monterey Peninsula Country Club and Poppy Hills). About 80% of the wastewater that enters the plant is sent to the golf courses and the remaining brine is sent to the ocean. Because every drop of water that can be reclaimed is one less drop that is discharged to the ocean we are always looking at ways to reduce discharges by modifying our processes and trying new technologies.
These seven golf courses receive nearly 100% of their irrigation water from CAWD. In 2018 alone this saved 1,028 acre-feet (over 330 million gallons) of water which did not need to be pumped from groundwater wells in the Carmel Valley River aquifer. This means more water for fish, trees and all the other riparian flora and fauna.
Turning Wastewater Into Energy
Over 99% of the waste stream that enters the plant is liquid. But there are solids in there too. These “solids” include bodily waste, fats, oils, garbage disposal waste, rinsed food, paper, hair, etc. These are processed separately from the liquids in five steps.
- Solids Settling. First, these heavier solids are allowed to slowly settle to the bottom of our large clarifier tanks.
- Digestion. Next, the settled solids (a slurry called “sludge”) are pumped from the bottom of the tanks to a 450,000-gallon anaerobic digester. Once inside the digester, the sludge is heated to at least 105 degrees and continually mixed for about 20-30 days. Helpful bacteria digest the solids under anaerobic (no oxygen) conditions. This process breaks down (i.e., “stabilizes”) the sludge to the point it will no longer putrefy (rot) if it is exposed to air.
- Pathogen Destruction. Disease causing pathogens, like viruses and harmful bacteria, evolved to thrive at the lower body temperature of animals. But the combination of higher temperatures and the 30-day digestion time destroys these pathogens.
- Methanogenesis. During the digestion process an amazing thing happens -- just like in our own intestines-- the bacteria make methane gas as a by-product. A lot of methane in fact; about 70% of the all the gas produced is highly flammable methane gas. The rest is carbon dioxide and trace amounts of other gases.
- Electricity Production. Prior to 2004 the methane gas was simply burned off in our flare without any benefit to the environment. Now the digester gas is compressed and fed to two micro-turbines. These burn the gas and spin small generators which produces electricity. To maximize electricity production and reduce the amount of gas flared, the District recently invested in a larger microturbine. We can now burn almost all the gas we generate which offsets about 15% of the plant's total electrical costs.
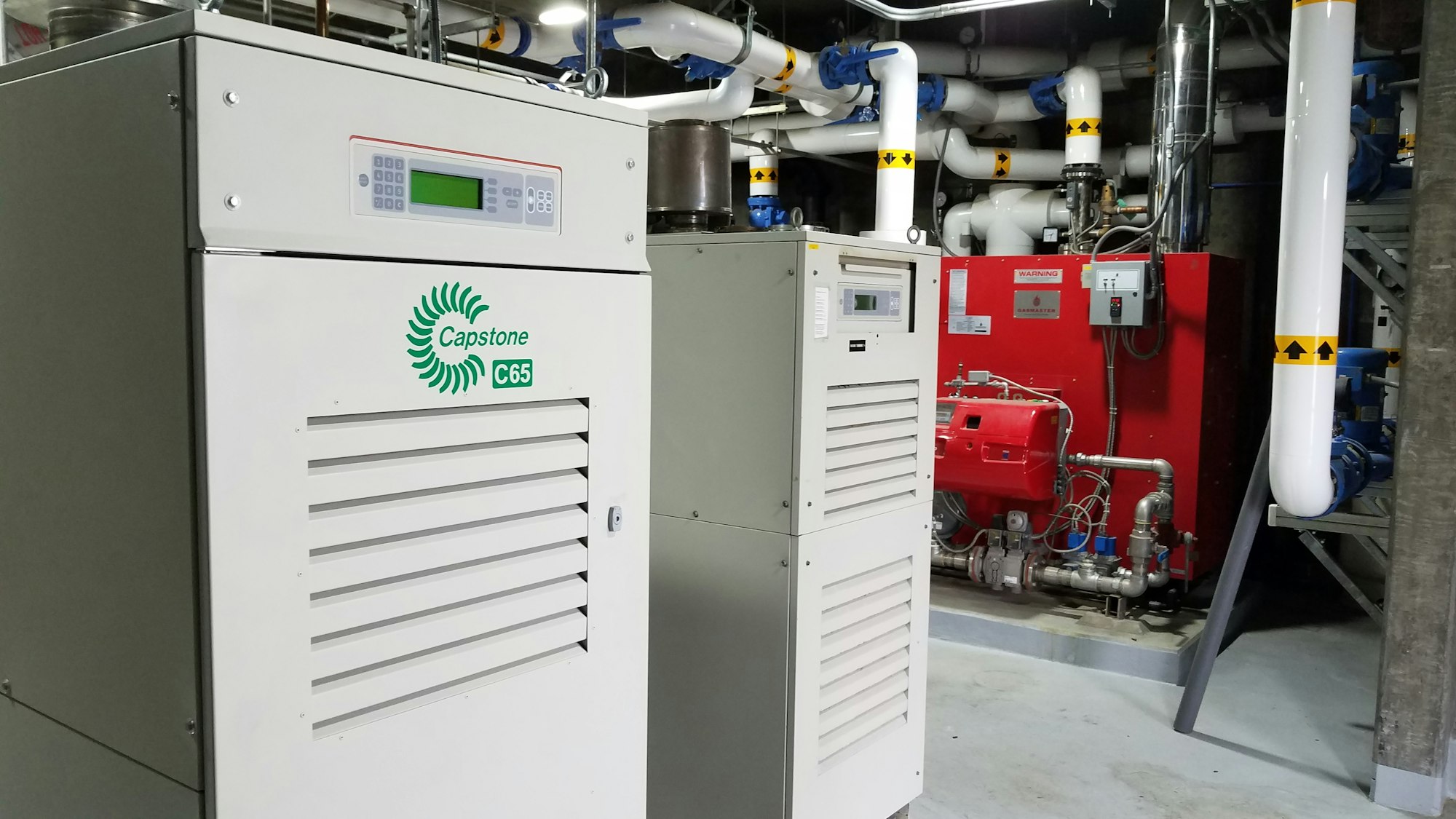
Turning Wastewater Into Fertilizer
About 20,000 gallons of stabilized sludge leaves the anaerobic digester each day. This must be handled properly to protect the environment. Many wastewater treatment plants simply spread the sludge out on the ground, allow it to dry, and then haul it to a landfill for disposal. This is both wasteful and is expensive. However, CAWD again finds a way to turn this waste into an environmentally friendly product.
- The stabilized sludge (about 5% solids and 95% liquid) is pumped to our dewatering building.
- There, the excess water is mechanically pressed out of the sludge resulting in a "cake" which is about 80% solids and 20% water.
- The resulting material is called “biosolids.” This is a black, moist material that is rich in organic material and very high in nitrogen.
- CAWD contracts with a company that hauls the biosolids to a compost operation in the Central Valley. Composters who start out with woody material need to add a nitrogen source to make more productive compost. By blending our biosolids into their compost they add more complex organics and nitrogen.
- CAWD tests the biosolids for all the legally required contaminants -- especially heavy metals -- to ensure it meets state standards and is safe for use in composting operations. Because our wastewater comes from domestic and light commercial sources, our biosolids are not high in metals like some cities with industrial or heavy commercial sources.
In summary, instead of being buried in a landfill, about 1,600 wet tons (or 260 dry tons) per year of biosolids are used to make better compost for crops.
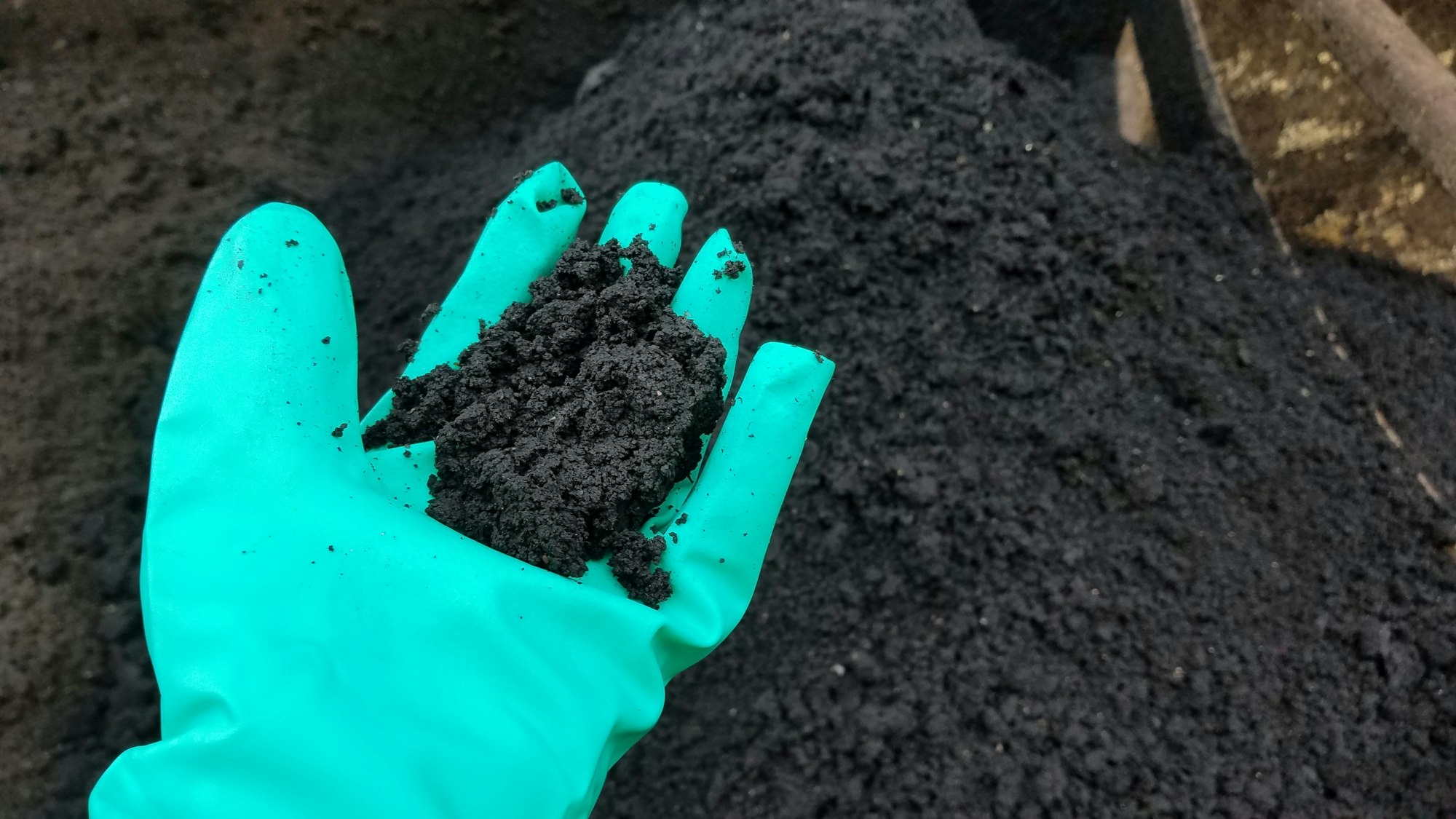